Ensuring safety during your pressure cleaning projects is paramount, especially in Australia where adhering to local regulations is crucial. I have reviewed the pressure cleaning guides from Safe Work Australia and, based on my 12 years of cleaning experience, I have laid out this best practice guide for carrying out pressure cleaning services in Australia. Documenting your procedures and implementing a quality management system are essential steps to minimize risks. In this post, I explain key safework methods and demonstrate how to create an effective work method statement using tools like Microsoft Word. By following these guidelines, you can achieve effective pressure cleaning while maintaining high safety standards for both residential and commercial properties. This approach not only protects your investment but also ensures long-lasting, spotless results.
Key Takeaways
- safety is essential during all pressure cleaning operations
- regular maintenance of equipment prevents accidents and ensures efficiency
- proper protective gear safeguards against debris and chemical exposure
- conducting thorough risk assessments minimizes potential hazards
- selecting appropriate pressure settings protects various surfaces from damage
Safe Methods for Effective Pressure Cleaning at Residential and Commercial Properties
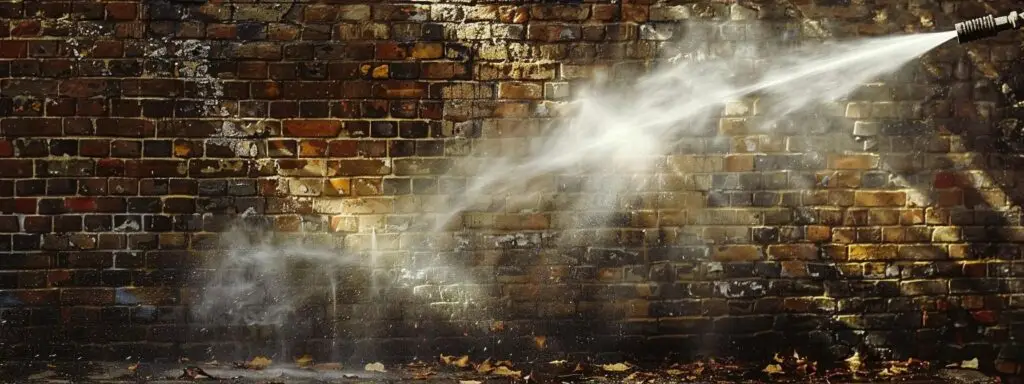
In my experience, ensuring safety during pressure cleaning is paramount. Recognizing potential hazards in various settings, from construction sites to residential carpentry projects, helps prevent accidents. Wearing appropriate personal protective equipment and understanding the pressure levels required for different surfaces are essential practices for effective and secure cleaning.
Understanding the Importance of Safety in Pressure Cleaning
From my observations, regular maintenance of cleaning equipment such as pumps and window cleaners is critical for safe operations. Ensuring that plumbing systems are free from leaks and that water pressure is appropriately regulated can prevent unexpected mishaps. By diligently inspecting and maintaining these tools, I can provide a safer and more effective cleaning service:
- Conduct routine checks on pressure pumps for wear and tear.
- Ensure that all plumbing connections are secure and leak-free.
- Calibrate water pressure settings based on surface requirements.
- Use designated cleaners for specific tasks to avoid chemical hazards.
- Train staff on the safe handling of all pressure cleaning equipment.
How to Carry Out Pressure Cleaning Safely at Homes and Commercial Sites
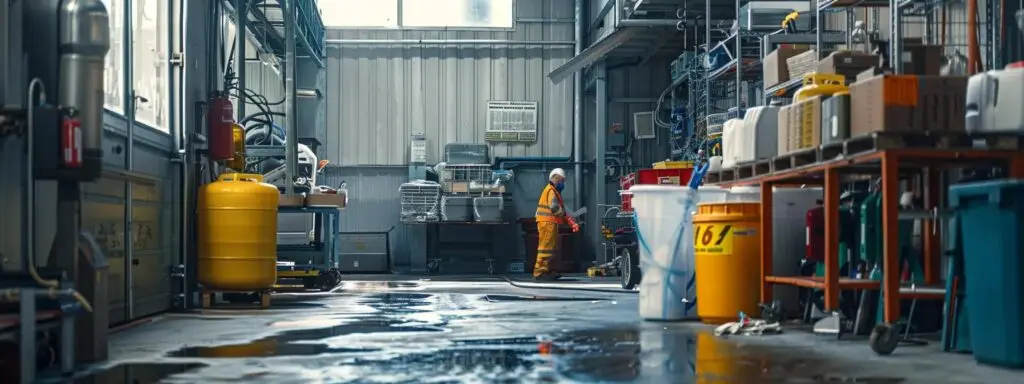
When performing pressure cleaning at homes or commercial sites, I prepare the area, choose the right equipment, and wear proper protective gear. I apply specific techniques for surfaces such as roofs and concrete to safely remove mold without causing damage. Effective management of the cleaning process also ensures compliance with insurance standards.
Preparing the Area Before Starting the Cleaning Process
Before I begin pressure cleaning a driveway or any other area, I conduct a thorough risk assessment to identify potential hazards that could impact health and safety. I use a cart to efficiently remove outdoor furniture, plants, and other obstacles, ensuring that nothing is left in the way that could be damaged or cause stains from the cleaning process. Additionally, I protect nearby surfaces and electrical outlets to maintain a safe environment for both the property and those using it.
Selecting the Appropriate Pressure Washer for Safe Use
When selecting the appropriate pressure washer, I prioritize models that comply with current legislation to ensure environmental and operational safety. Choosing the right equipment helps effectively eliminate mildew and dirt without causing water damage to surfaces. If you have any questions or need recommendations, feel free to reach out via email for personalized assistance.
Wearing the Right Personal Protective Equipment for Cleaning
Proper personal protective equipment is essential for safe pressure cleaning. I always wear protective glasses to shield my eyes from debris and ensure clear visibility during inspection. Additionally, I use gloves and sturdy footwear to protect against potential contact with rust on surfaces like sidewalks and the pressure washer’s tank:
Equipment |
Purpose |
---|---|
Protective Glasses |
Shield eyes from debris and water spray |
Gloves |
Protect hands from rust and chemicals |
Sturdy Footwear |
Avoid slips on wet sidewalks and protect feet from heavy equipment |
Techniques for Safe Pressure Cleaning on Different Surfaces
When approaching different surfaces, I rely on a comprehensive checklist to maintain safety and achieve optimal results. For instance, cleaning a car’s exterior requires lower pressure and specific gallons of eco-friendly detergent to avoid damage, while concrete areas can handle higher pressure settings. Utilizing tools similar to Microsoft applications helps me organize each job efficiently, ensuring that every step adheres to safety standards and delivers a thorough clean.
Cleaning Techniques to Avoid Damage During Pressure Washing
In my experience, adjusting the pressure settings is crucial when cleaning sensitive surfaces such as steel railings in apartment complexes or vehicles, ensuring no damage occurs during the process. I also refer clients to detailed PDF guides that outline step-by-step techniques, similar to safely maneuvering heavy equipment like a crane, to maintain the integrity of various materials while achieving a spotless finish.
Key Pressure Cleaning Safework Methods
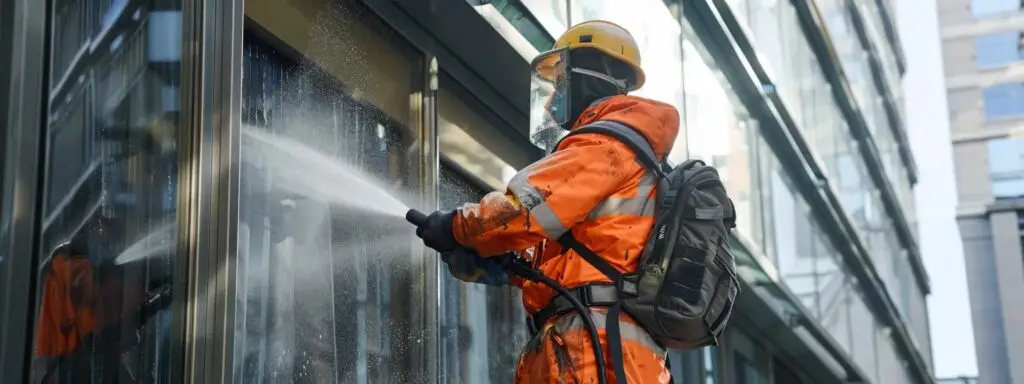
Establishing safe work practices for pressure cleaning involves using the right tools and ensuring trucks are properly equipped. Identifying hazards, such as handling dangerous goods and operating washing machines, allows for effective control measures. Additionally, comprehensive training and adherence to industry standards are essential for the safe operation of pressure cleaning equipment.
Establishing Safe Work Practices for Pressure Cleaners
Establishing safe work practices for pressure cleaners begins with selecting the correct nozzle and ensuring all gear is in optimal condition. When working in environments like parking lots, it’s essential to adjust the nozzle to effectively remove algae without causing surface damage. Maintaining a safe workplace also involves regular equipment inspections and adhering to safety protocols, which I prioritize to deliver reliable and secure pressure cleaning services.
Identifying Hazards and Implementing Control Measures
In my experience, identifying potential hazards such as wet curbs, crowded warehouses, faulty air conditioning systems, and active plant areas is essential for implementing effective control measures. By thoroughly assessing each site and addressing these risks, I ensure a safe and efficient pressure cleaning process for every project:
Setting | Hazard | Control Measure |
---|---|---|
Curb | Slippery surfaces from water spray | Use non-slip footwear and place warning signs |
Warehouse | Cluttered areas causing trip hazards | Clear pathways and organize equipment before cleaning |
Air Conditioning Units | Electrical risks near water sources | Ensure all electrical connections are secured and isolated |
Plant | Exposure to chemicals and high-pressure equipment | Provide appropriate protective gear and training to staff |
Training and Standards for Safe Operation of Pressure Cleaning Equipment
In New Zealand, I ensure that all pressure cleaning staff receive thorough training on handling emergencies and safely managing sites with asbestos, which is crucial for maintaining the integrity of our services and honoring warranties. By adhering to stringent industry standards and integrating pest control considerations, we provide reliable and compliant pressure cleaning solutions that protect both properties and their occupants.
Creating and Using a Safe Work Method Statement for Pressure Cleaning
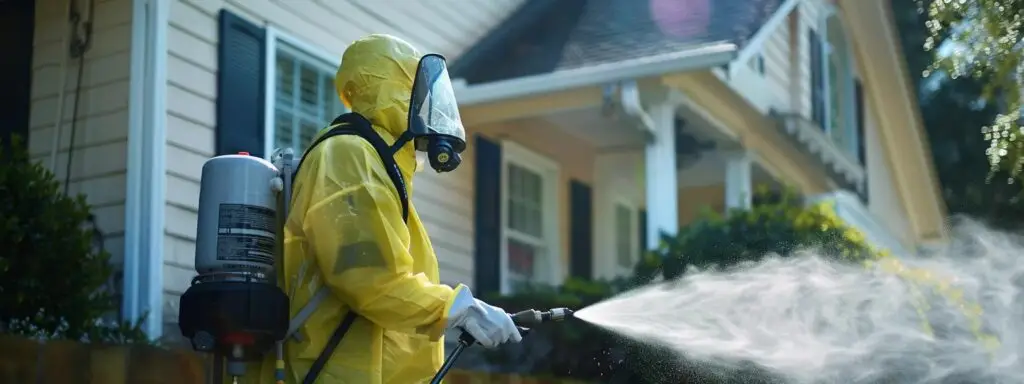
An effective Safe Work Method Statement (SWMS) encompasses key components such as hazard identification, risk assessment, and implementation of control measures. Customizing your pressure cleaning SWMS for specific jobs like forklift operation, scaffolding use, or demolition tasks ensures tailored safety protocols. Utilizing a SWMS helps prevent injury and leverages industry insights from sources like Reddit.
Key Components of an Effective Safe Work Method Statement
Crafting an effective Safe Work Method Statement involves detailing each step of the pressure cleaning process, from the proper operation of machines to the safe transport of equipment. I ensure that every contract includes protocols for managing waste to protect curb appeal and the surrounding environment. By clearly outlining responsibilities and safety measures, we maintain high standards and prevent accidents during every project.
Customizing Your Pressure Cleaning SWMS for Specific Jobs
When customizing my Pressure Cleaning SWMS for specific jobs, I take into account factors such as controlling noise levels in residential areas, effectively removing graffiti with specialized techniques, and implementing robust waste management practices. I also prioritize using environmentally friendly cleaning agents to protect the surrounding ecosystem and ensure the safe removal of lichen from various surfaces. This tailored approach allows me to address unique challenges efficiently while maintaining high safety and quality standards.
Benefits of Using a SWMS in Pressure Cleaning Operations
Implementing a Safe Work Method Statement (SWMS) in pressure cleaning operations significantly enhances safety and efficiency when working with various surfaces such as masonry, brick, and metal. By outlining specific procedures for using ladders and handling delicate materials like carpet, a SWMS helps prevent accidents and ensures that each job is carried out effectively. This structured approach not only protects workers but also maintains the integrity of the properties being cleaned.
Pressure Cleaning SWMS Template and Its Utilization
Hi! I would like to share with you how to create a Safe Work Method Statement (SWMS) Template for Pressure Cleaning. This template will help us stay safe while cleaning with a pressure washer.
Columns
First, let’s set up the columns in Excel. These columns will help us organize all the important information.
Column | Description |
---|---|
Task No. | A unique number for each task. |
Task Description | What the task is about (e.g., “Set up pressure washer”). |
Hazards | Possible dangers (e.g., “Electric shock from equipment”). |
Risk Assessment | How risky the hazard is (Low, Medium, High). |
Control Measures | Steps to make the task safer (e.g., “Use Ground Fault Circuit Interrupter”). |
PPE Required | Personal Protective Equipment needed (e.g., gloves, goggles). |
Responsible Person | Who is in charge of the task. |
Emergency Procedures | What to do in case of an emergency. |
Training Required | Any training needed to do the task safely. |
Sign-Off | Space for signatures to confirm the task was reviewed. |
Sample Entries
Task No. | Task Description | Hazards | Risk Assessment | Control Measures | PPE Required | Responsible Person |
---|---|---|---|---|---|---|
1 | Site Setup | Tripping hazards from equipment | Medium | Clear workspace, use warning signs | High-visibility vest, gloves | Site Supervisor |
2 | Equipment Inspection | Equipment failure | High | Inspect pressure washer before use | Gloves, safety glasses | Technician |
Download Templates and Sample
Final Tips
Regular Reviews: Check and update the SWMS often to keep it accurate.
Training: Make sure everyone knows how to use the SWMS and understands their roles.
Accessibility: Keep the SWMS in a place where everyone can access it.
Compliance: Make sure our SWMS follows local safety rules and standards.
Post-Cleaning Safety and Maintenance Considerations
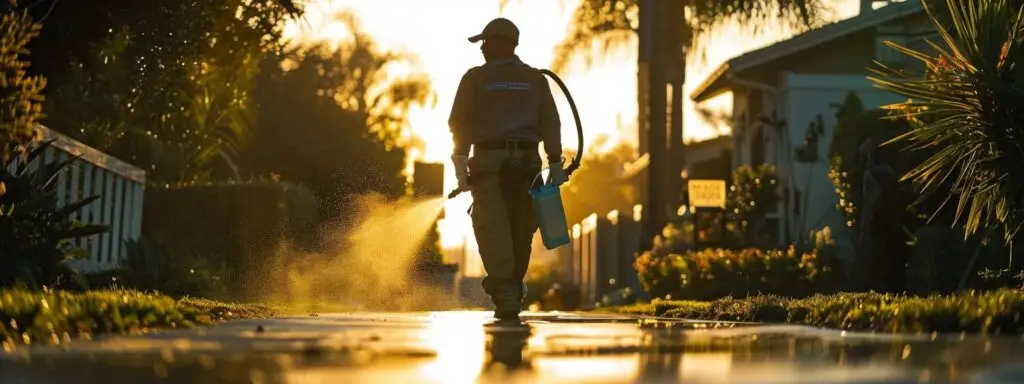
After completing pressure cleaning, I ensure site safety by adhering to regulatory compliance and quality management standards. I provide maintenance tips for pressure cleaning equipment to extend their longevity and effectiveness. Additionally, I evaluate the cleaning process’s success, addressing areas like gas streams and plumbing fixtures such as toilets to ensure thorough and lasting results.
Ensuring Site Safety After Completing Pressure Cleaning
After completing pressure cleaning projects in Texas, I make sure patios are thoroughly cleared of oil residues and any remaining debris. This attention to detail ensures that each customer enjoys a safe and immaculate outdoor space. Properly maintaining the scrubber and other equipment prevents future issues and supports long-lasting results:
Task | Details |
---|---|
Inspect Cleaned Areas | Check patios and surrounding spaces for any missed spots or oil residues. |
Clean Equipment | Thoroughly clean the scrubber to remove all oil and debris, ensuring optimal performance. |
Secure Storage | Store all tools and machines safely to prevent accidents and extend their lifespan. |
Customer Walkthrough | Review the cleaned areas with the customer to ensure satisfaction and address any concerns. |
Final Safety Check | Ensure all electrical outlets and nearby surfaces are dry and free from hazards. |
Maintenance Tips for Pressure Cleaning Equipment
Regular housekeeping and diligent maintenance are crucial for sustaining the performance of pressure cleaning equipment, especially in environments that involve heavy equipment, welding, or are part of manufacturing and factory operations. After each use, I meticulously clean all components to remove any debris or residue that could impair functionality. Additionally, I schedule routine inspections to detect and address any signs of wear or damage early, ensuring that the equipment remains reliable and efficient for all your cleaning needs.
Evaluating the Effectiveness of Your Cleaning Process
To evaluate the effectiveness of my cleaning process, I carefully inspect each surface using a squeegee to ensure all debris is removed and employ a mop to eliminate any remaining soap residues. Additionally, I utilize JavaScript-based tools to track cleaning performance and gather data for continuous improvement. This thorough evaluation guarantees that every job meets high standards:
- Use a squeegee to check for leftover debris on surfaces.
- Mop areas to remove any residual soap and ensure a spotless finish.
- Implement JavaScript tools to monitor and analyze cleaning performance.
Hire Professional pressure cleaning services
Safety is paramount when it comes to pressure cleaning. Instead of opting for a DIY approach, hiring professionals ensures that the job is done safely and efficiently. I recommend utilizing Alliance Pressure Services that adhere to the best industry practices and comply with all Occupational Health and Safety (OHS) procedures. Below are links to their professional pressure cleaning services operating in five major Australian cities:
- Sydney Pressure Cleaning
- Melbourne Pressure Cleaning
- Brisbane Pressure Cleaning
- Perth Pressure Cleaning
- Gold Coast Pressure Cleaning
By choosing these professionals, you ensure that your pressure cleaning is performed to the highest standards, adhering to all OHS guidelines. They operate across Sydney, Melbourne, Brisbane, Perth, and the Gold Coast, providing reliable and expert services tailored to both residential and commercial needs. Trusting the experts not only safeguards your property but also delivers impeccable and lasting cleanliness.
Frequently Asked Questions
What safety equipment is essential for pressure cleaning?
When pressure cleaning, I always wear essential safety gear such as protective goggles to shield my eyes, durable gloves for hand protection, sturdy non-slip footwear to prevent falls, and hearing protection to mitigate noise exposure.
How can I prevent surface damage during pressure cleaning?
To prevent surface damage during pressure cleaning, I use the correct pressure settings, maintain a steady distance from the pavers, and choose cleaning solutions specifically designed for outdoor surfaces. This approach ensures effective cleaning without harming your outdoor pavers.
What steps are involved in a safe pressure cleaning process?
In a safe pressure cleaning process, I begin by inspecting the surface and choosing the right pressure level. Next, I protect surrounding areas, apply suitable cleaning agents, use the pressure washer with steady movements, and finish by thoroughly rinsing to ensure a clean, damage-free result.
How Do I Create a Safe Work Method Statement for Pressure Cleaning?
To create a safe work method statement for pressure cleaning, identify potential hazards, implement control measures, specify necessary equipment and personal protective equipment (PPE), outline step-by-step procedures, and ensure all personnel receive proper training and understand emergency protocols.
What maintenance is needed after pressure cleaning?
After pressure cleaning, regularly inspect and remove debris, apply sealants to protect pavers, ensure proper drainage, and clean gutters to prevent water damage. Schedule periodic maintenance cleanings to preserve surface quality and longevity.
Other Helpful Pressure Cleaning Articles
Enhance your pressure cleaning knowledge and stay updated with best practices by exploring the following articles:
- Comprehensive Guide to Pressure Cleaning Services
- Benefits of Professional Pressure Cleaning
- How to Choose the Right Pressure Cleaning Service
- Pressure Cleaning Maintenance and Care
- Environmental Impact of Pressure Cleaning
- Latest Pressure Cleaning Technologies
- Pressure Cleaning Methods
These resources provide valuable insights into various aspects of pressure cleaning, from selecting the right service to understanding the environmental implications and the latest technological advancements. Whether you’re a homeowner or a commercial property manager, these articles will help you make informed decisions and maintain high standards in your pressure cleaning projects.
Conclusion
Ensuring safety in pressure cleaning is essential for both residential and commercial properties. By consistently maintaining equipment, wearing proper protective gear, and adhering to tailored safety protocols, I prevent accidents and achieve superior cleaning results. Training staff and implementing comprehensive Safe Work Method Statements further enhance the effectiveness and reliability of our services. Prioritizing these safe methods not only protects property and personnel but also reinforces trust and satisfaction among clients.